工場レイアウトは、動線から考えると上手くいく
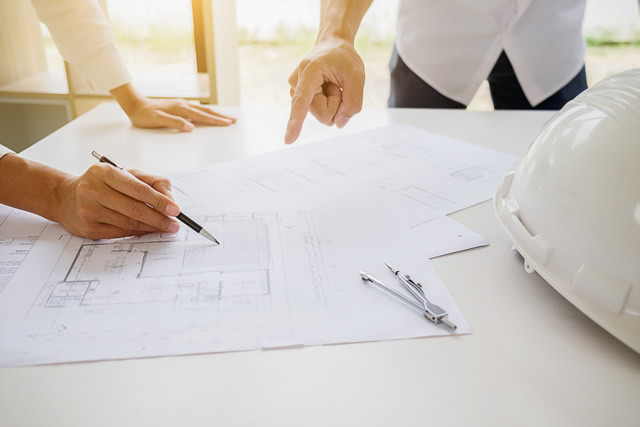
工場内のレイアウトを改善すると、ちょっとしたミスが減り、業務効率を上げられるかもしれません。
今回は工場におけるレイアウトの改善ポイントや、具体的な改善方法・手順を順番にご説明します。
目次 [非表示]
1.工場のレイアウトが起こす問題
業務の流れを意識した工場レイアウトは作業効率の向上に繋がりますが、能率的に配列されていないレイアウトはさまざまな問題を引き起こす要因となります。
例えば、通路の動線が錯綜し、人の動きが重なり合う通路があると接触事故の可能性が高まります。また、保管エリアと出荷エリアが不明瞭なために引き起こされる出荷ミス、関係部署間の距離が遠くて起こる伝達ミスなどが挙げられます。
このように、非効率なレイアウトは知らないうちにミスを引き起こす可能性があるため、工場内の設備・エリア配置を工夫する必要があります。
2.レイアウトの改善は動線から
実際にレイアウトを改善する場合、何よりも動線を意識して設計することが大切です。
動線は、作業員や商品が移動する流れを指します。不必要に長い動線は時間的なロスの原因となり、狭い動線は接触事故を招くなど、動線を意識していないレイアウトは作業上のリスクを高めてしまいます。
作業効率改善だけでなく、事故を未然に防ぐためにも動線を意識してレイアウトを考える必要があります。自社工場の動線には問題がないか、以下のチェックポイントを確認してみましょう。
・通路の幅は十分か、安全確保はできているか
・多くの動線が重なり合っていないか
・頻繁に使う設備やエリアまでの距離が適切か
・生産量の多い商品の動線が不必要に長くないか
動線を改善することで作業場のミスを減らせる可能性があります。
3.作業効率・保管効率を高める
工場内の動線を確認したら、次はそれぞれの作業場が効率よく業務を行える配置になっているかを確認していきます。
効率を意識して工程順に設備・エリアを配置すると、商品移動時の紛失や破損の防止に繋がります。また、道具や備品がすぐに取り出せるように保管されていると、時間ロスを防止できます。
自社の工場レイアウトは効率を重視した配置になっているか、以下のポイントを確認してみましょう。
・棚や高さを有効活用して保管が効率的に行われているか
・作業工程に合った設備配置がされているか
・使用頻度や使用場所に対して備品の保管場所は適切か
・製品や備品は取り出しやすく整理整頓されているか
適切な場所への配置は、作業効率の改善はもちろん、商品の破損や紛失といったリスクの抑止に繋がるのです。
4.部門別のエリア分け
適切なレイアウトを構築するには、工場全体を俯瞰して部門別に配置を考えることも重要です。
エリア設計が上手にできていると、いろいろなメリットがあります。例えば、部外者の出入りが多い部門を入口付近に配置するとセキュリティの向上に繋がり、緊密な連絡を取り合う部署を隣接して設置すると、報告漏れや伝達ミスのリスクも減らせます。
工場内のエリア配置が適正かどうかは、以下のポイントから確認できます。
・出入りの頻度にあった位置にあるか
・同一作業者・管理者のエリアが離れていないか
・工程に沿った配置になっているか
・重量があるものや危険物の移動は容易か
・騒音や振動、埃など隣接エリアへの影響はないか
エリアは容易に変更できないケースが多いため、慎重に確認していきましょう。
5.工場レイアウトを改善する8つの手順
最後に、工場のレイアウト変更を実際に行う場合の具体的な手順をご紹介していきます。
手順①.全体のスペース調査
手順②.動線の分析
手順③.全体の物量を把握
手順④.業務の流れに沿う設備の配列を検討
手順⑤.レイアウト相関の分析と設計
手順⑥.レイアウト変更の実施
手順⑦.レイアウト改善の効果検証・調整
手順⑧.レイアウトを定着化させる
手順①.全体のスペース調査
まずは、改善箇所のレイアウト図を入手して面積を把握し、デッドスペースになっている場所はないか確認します。
デッドスペースの調査は、平面ロス(ものが置かれていない)・高さロス(高さを有効的に使えていない)・山欠けロス(棚を有効的に使えていない)の3つの観点から行いましょう。
手順②.動線の分析
次に、人や商品の動き方を把握し、動線の分析を行います。
商品ごとに業務の流れを可視化したシートを作成してレイアウト上に業務の流れを書き込み、改善後と比較するために現状の動線の長さを計測します。この時、2章でお伝えした動線のチェックポイントも同時に確認しておきましょう。
手順③.全体の物量を把握
動線を改善するときに優先する重点商品を決定するため、商品ごとの物量を確認します。販売量・入出荷件数などをもとに重点管理対象となる商品を決定し、該当商品には優先的に動線を割り振っていきます。
手順④.業務の流れに沿う設備の配列を検討
人やものの動きを確認し、業務過程が似ているグループは近くに配置します。この時、手順②の動線分析で使用した商品ごとの業務過程シートを使用すると効率的です。
手順⑤.レイアウト相関の分析と設計
分析が完了したら、実際のレイアウト構想を図面に落とし込みます。手順①から④までのデータを踏まえ、設備や部署をどのように設置するかを決めましょう。
手順⑥.レイアウト変更の実施
レイアウト図が完成したら、実際にレイアウトを変更するスケジュールを決定、実施します。実施には担当者を選定して、計画通りに進んでいるか進捗状況を逐一確認すると、スムーズかつ漏れなく進められます。
手順⑦.レイアウト改善の効果検証・調整
レイアウトの変更が終わったら、実際に作業を行います。その際、問題点が改善されているか、レイアウトを変更したことで新たにミスが発生していないかをチェックします。結果を検証しつつ、新たな課題が見つかれば改善に取り組んでいきます。
手順⑧.レイアウトを定着化させる
十分にPDCAを回したら、レイアウトを定着させます。細々とした改善は順次行う必要がありますが、大きな配置変更が続けば作業員が混乱しミスを引き起こすケースも想定されます。大きな配置変更を最小限に抑えるために、手順に沿って事前調査をしっかりしてから改善しましょう。
6.まとめ
工場のレイアウトが適切な状態になると、従業員の安全性の確保や生産性の向上につながります。
レイアウトを変更する場合は動線の改善を優先し、次に作業効率の改善、エリア分けを行います。ご紹介した手順を踏んでレイアウト変更を行い、作業員が働きやすい工場を目指しましょう。